Services
Partners in Success
End-to-end metal forming services built upon long-term partnerships with our customers.
Interlaken offers a wide array of services in part production and part development. We will lead you through initial observations, discovery, innovation review, proof of principle, best option, and production readiness to bring your design from concept to reality. We call this, Solutioning. We’re here to partner with you long-term, to support your continued growth and success.
Part Production
Hydroform Parts
Hydroforming begins where traditional manufacturing processes end. Hydroform components simply perform better and allow for greater design flexibility. ITC helps you overcome quality issues, reduce cost, and lower component part counts. Our engineers determine the maximum forming pressure necessary and component material thinning. For many applications, hydroforming just makes sense. Tube hydroforming reduces weight and increases strength and stability.
Elevated Temperature Forming
The press and forming system components are analogous to traditional fluid hydroforming. Instead of water pressure, gas pressure is used to form aluminum alloys in a heat softened state. The addition of temperature allows parts to be made using far less force with very little springback effect. Economical tools focus on forming parts rather than controlling massive forming pressures. Expansion or forming ratio limits are no longer a significant design constraint. Highly accurate control over temperature, pressure and force application enable the process to provide shapes and feature details never imagined in traditional cold forming of many aluminum alloys.
Advantages of Using ITC to Produce Your Parts
ITC starts with a Concept Consultation. We work with you to identify needs, wants, and expectations. Then comes metal formability testing, Finite Element Analysis (FEA), tooling design, and prototyping. Finally we create the tooling, and from there ITC will begin producing your parts.
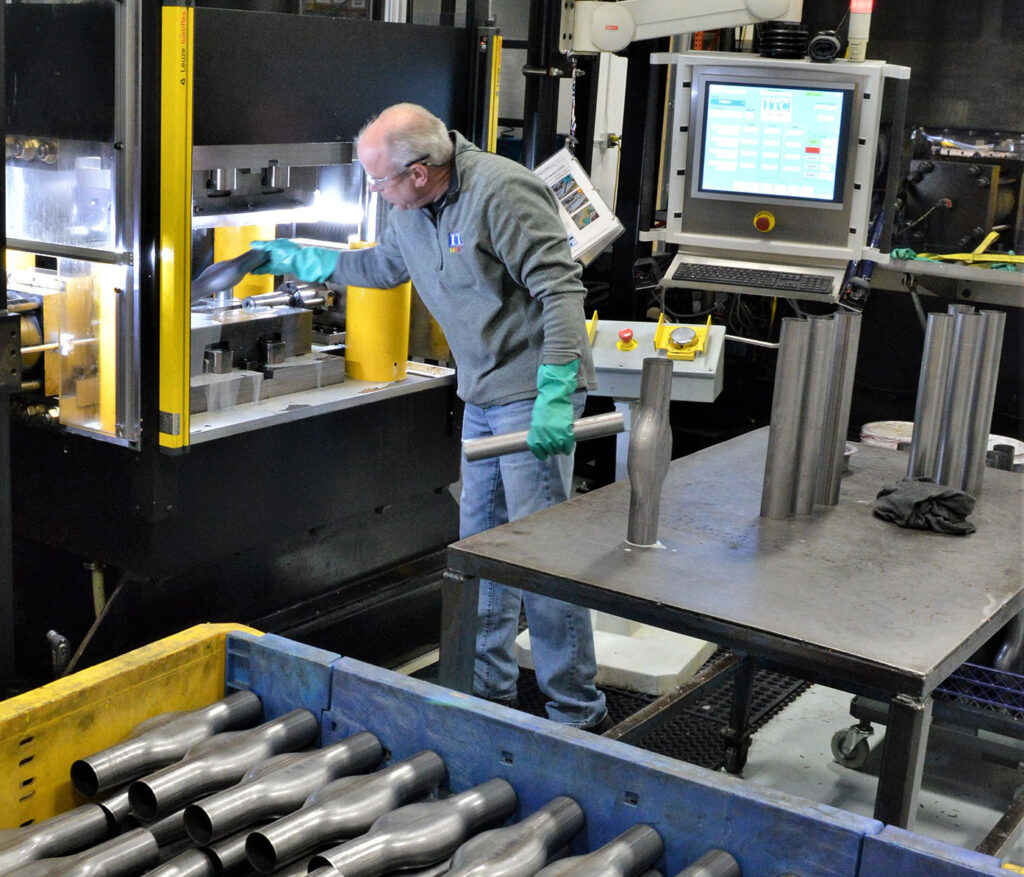
Part Development
ITC takes the designs, models, FEA output, and what we’ve learned about the transition from blank to final part, to prepare for a move into the physical world. We’ll create tools, develop the forming recipe, use your chosen material, and make the part. This is a prototype. The learning process continues as we try to verify all that was revealed in FEA. Did the part preform correctly? Was it the correct pressure and feed profile? We’ll run iterations until we’ve proven our theory and your part is successfully being produced.
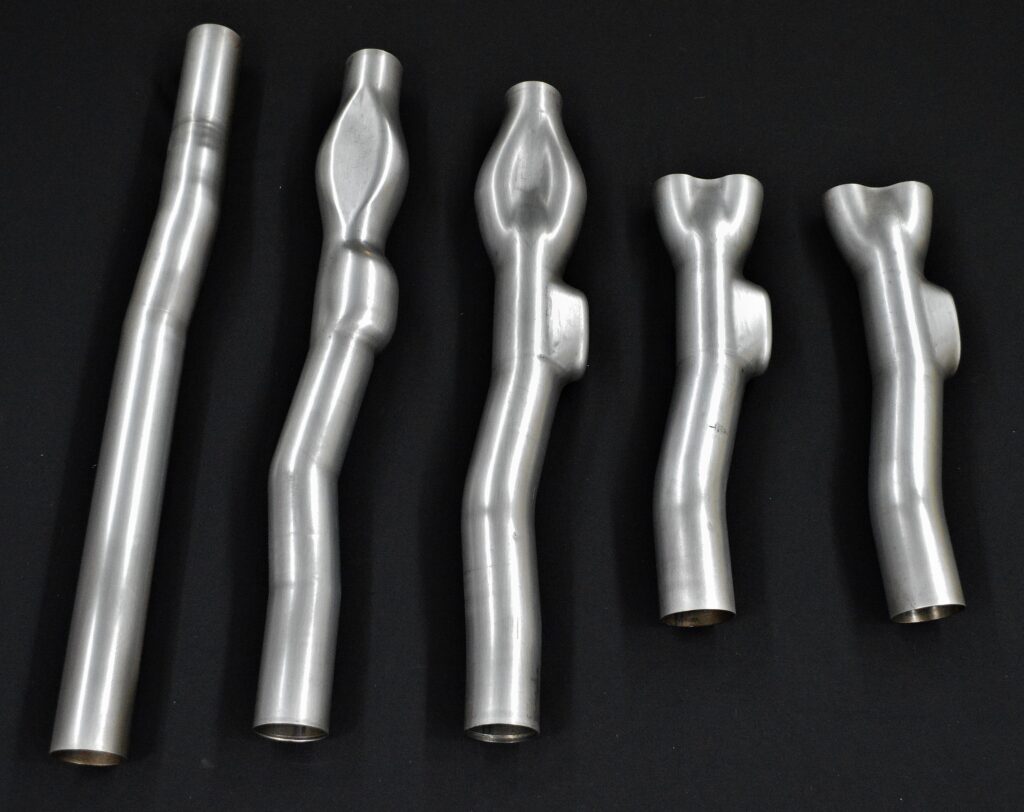
FEA Simulation
Hydroforming is a biaxial deformation process, so simulation accuracy is improved when a biaxial model of material properties is utilized. ITC’s path to success is built on Finite Element Analysis (FEA) simulation. We’ll determine the validity of using a particular part geometry, material and wall thickness. We’ll work to learn and understand the material behavior, strain states, and thinning. At this point we can make recommendations on possible changes to part geometry to best utilize the hydroforming process. It’s all about ensuring that your part does what it needs to.
Using FEA, we can swiftly perform a variety of measures and analyses with good precision. This leads to informed decisions on necessary press forces, forming forces, and hydroforming pressures specific to your application. There’s no need to build and test when ITC can simulate and prototype. Especially when we meet performance criteria on the first try.
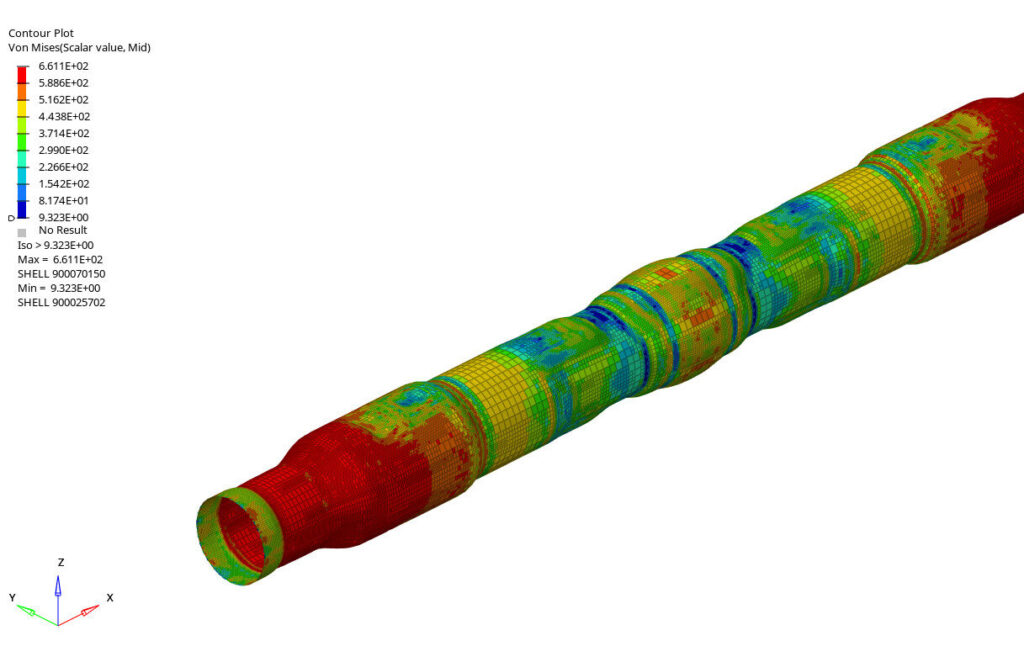
Material Testing & Selection
To help you choose the right material, Interlaken will evaluate the requirements of the transformation. We’ll look at the length of line of the blank compared to the final length of line of the part. This includes the diameter of the tube at the beginning compared to the diameter of the part shape upon completion. Length of line is used because the final shape is not always a circle. The transformational change in a room temperature or elevated temperature process is still limited to certain material properties.
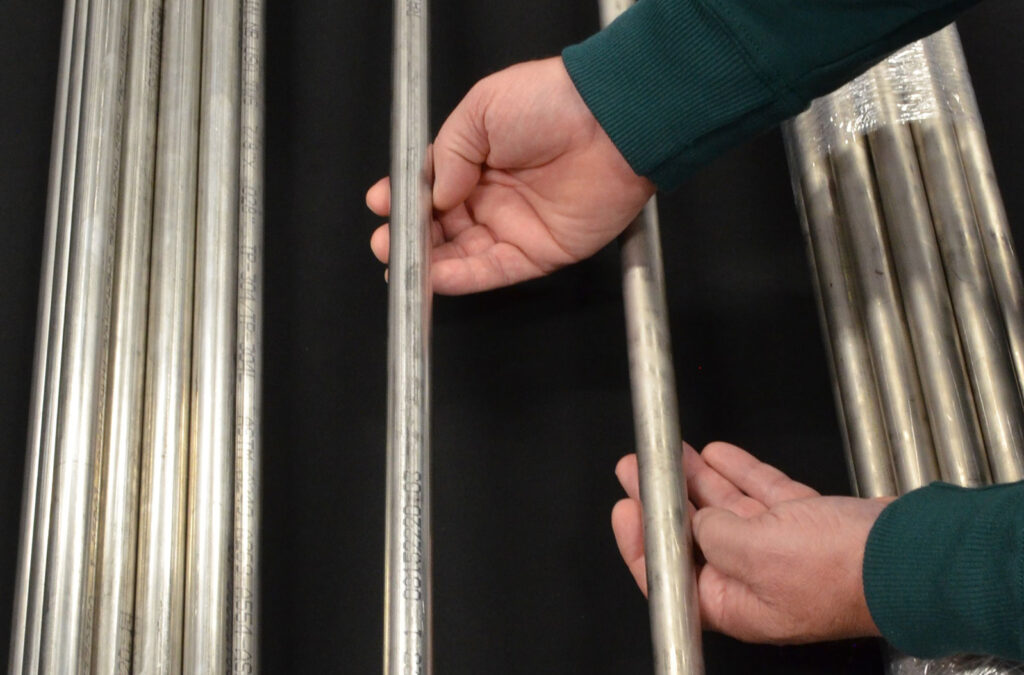
Product & Tool Design
ITC people possess the skills and abilities to help you achieve your goals. We’ll work with you as a partner, encouraging you to lean on us. ITC engineers will collaborate with you to develop, test, analyze, prototype, and validate your design. At the same time we’ll search for a better and more cost effective way to solve the problem. We don’t just listen; we’ll hear you and advise you. ITC utilizes DFM and DFA process strategies for turn key tooling solutions. Be it a preform, a bend, a crush, or a final hydroform, we will design tooling and forming dies for the necessary steps to produce your final part. Don’t worry if you have little or no knowledge of tooling. ITC does and we’re here to help you succeed.
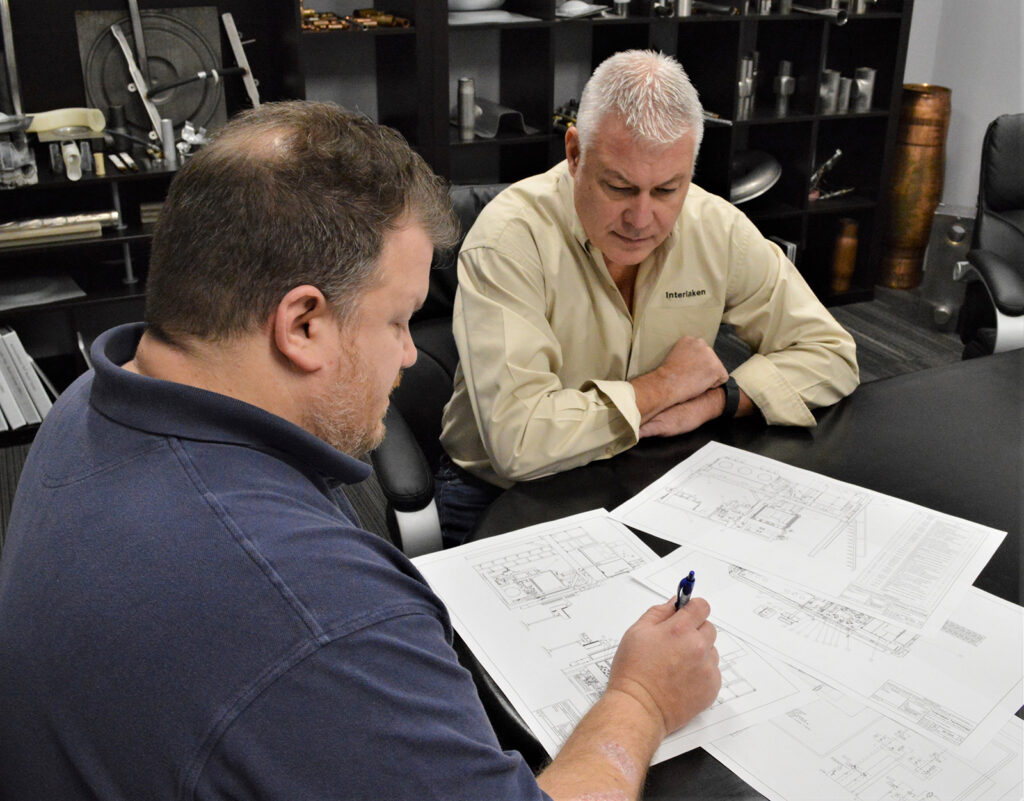