Services
We make it
Systems
You make it
Redefining the Possible
Forming seemingly impossible shapes with the utmost part consistency.
The ITC Edge
For nearly 45 years, ITC has consistently redefined what’s possible. From our roots as a manufacturer of transducers and load cells to our current advanced metal forming system design and production. ITC systems leverage exclusive technology to form unique and complex shapes with great part consistency. Whether you’re looking to outsource your part production, bring it in-house with a custom solution or a combination of both, ITC will make your vision a reality.

Partners in Success
End-to-end metal forming services built upon long-term partnerships with our customers.
ITC Services
Part Production
ITC engineers are all about challenging the norms to find new ways to produce parts. Our systems are designed to meet the needs of the customer. We specialize in optimizing system size and performance, for the specific requirements necessary. Solutions driven by cost effective tooling is what sets Interlaken apart.
Part Development
ITC starts with a product design consultation. We work with you to identify needs, wants, and expectations. Then comes metal formability testing, Finite Element Analysis (FEA), tooling design, and prototyping.
FEA Simulation
Finite Element Analysis is used as a one-step simulation for feasibility assessment. We’ll determine the plausibility of using a particular material, wall thickness, and part geometry. We’ll develop an understanding of the material behavior, strain states, and thinning. Customers continue to be impressed with ITC’s ability to rapidly validate designs and promptly release into production.
Material Testing & Selection
To help you choose the right material, Interlaken will evaluate the requirements of the transformation. We’ll look at the length of line of the blank compared to the final length of line of the part. This includes the diameter of the tube at the beginning compared to the diameter of the part shape upon completion.
Product & Tool Design
ITC engineers will collaborate with you to develop, test, analyze, prototype, and validate your design. Be it a preform, a bend, a crush, or a final hydroform, we will design tooling and forming dies for the necessary steps to produce your final part.
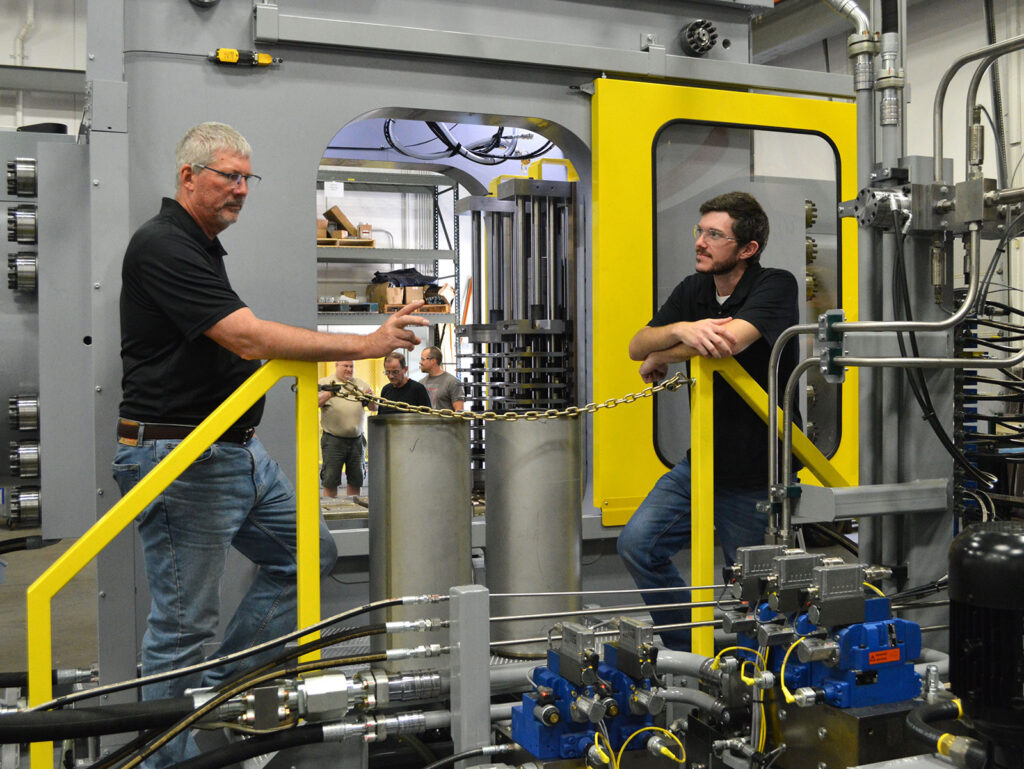
Committed to Excellence
Standard and custom hydraulic press systems designed to deliver exceptional production and testing outcomes.
ITC Systems
Hydroforming
ITC specializes in production tube hydroforming systems up to 2000 tons. The intensifier(s), feed actuators and custom tooling meld to produce high quality parts.
Material Formability
ITC has seven standard models of precision controlled hydraulic ServoPress. Evaluate sheet and tube forming properties, rank lubricants or use elevated temperature for product development or quality control.
Elevated Temperature
Interlaken’s expertise lies in the elevated temperature forming of aluminum tubes. Elevated temperature is utilized to increase formability and decrease pressures and forces compared to room temperature.
Pressure/Burst Testing
Standard pressure/burst testing systems are available up to 100,000 psi (7000 bar). ITC’s proficiency in ultra-high pressure and high force hydraulics leads to precision, repeatability and dependability.
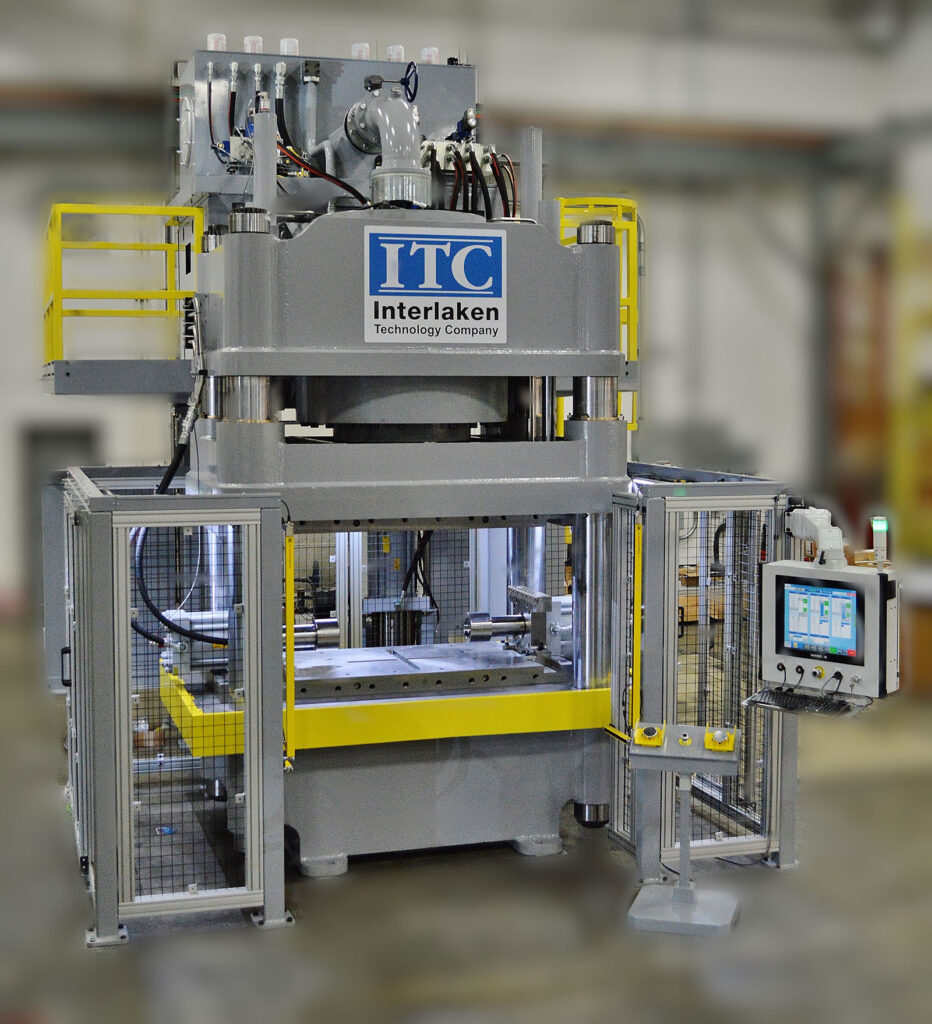
Globally Driven Expertise
ITC installations enable advanced metal forming on a global scale.